外部实时位置及定位控制电路提高工业机器人的轨道精度
esd EtherCAT网桥产品ECX-EC被使用在此系统中,用来连接PC和机器人控制系统。
德国弗劳恩霍夫生产技术和应用材料研究所(IFAM)在CFK NORD研究中心研制出提高工业机器人精度的方法,以便工业机器人能运用于飞机制造中的大型结构切削加工中。
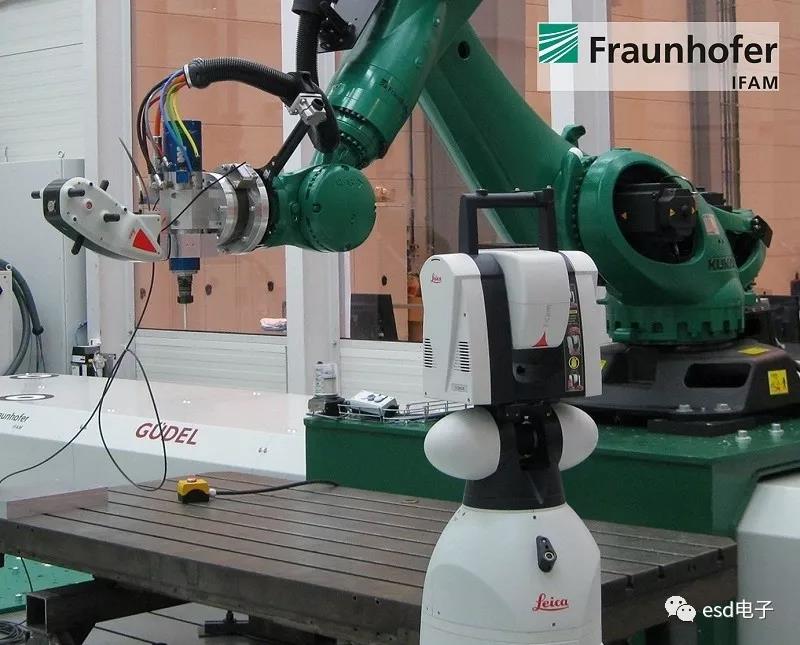
相较于目前使用的大型机床,六轴工业机器人在此领域更有优势,因为机床相对较昂贵,沉重,并且某些机床并不灵活。虽然工业机器人配备以高频铣床主轴,原则上来说适用于CFK(碳纤维增强塑料)切削加工,但是其目前还未达到飞机制造要求的轨道精度。轨道错误分为静态位置错误及动态位置错误。静态位置错误通过机器人的校准即可大大消除(此过程中限制因素是机器人的重复精度),而动态位置错误必须实时发现,通过外部的位置控制电路克服。在CFK切削加工过程中,动态位置错误主要归结于如机械机器人结构的弹性形变,特别是与切削力有关的变速器弹性形变造成的。
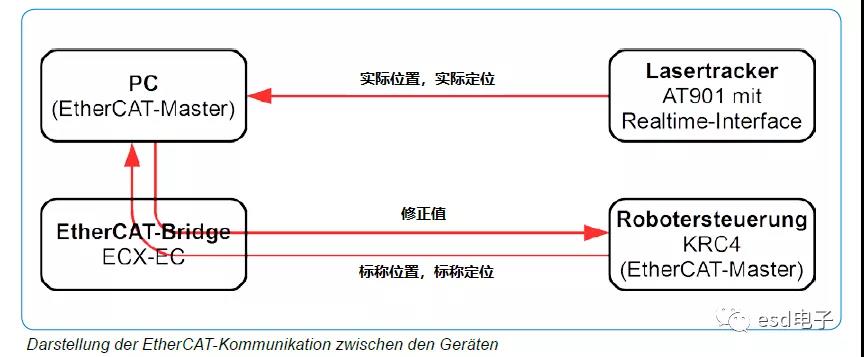
弗劳恩霍夫生产技术和应用材料研究所(IFAM)研制了一个外部控制电路,借助当下的标称位置和实际位置,实时地在计算机上计算出位置错误。当下的标称位置由机器人的控制装置计算出并传输至计算机,当下的实际位置则由激光跟踪器测量。电子调整算法会将机器人每条轴的动态特点考虑在内,得出修正值,传输给机器人控制系统以弥补位置错误。
此解决方法的优点是,尽可能地既收集到了静态错误和影响,又收集到了动态错误和影响,比如计算机控制系统使用的运动学模型错误,弹力变形错误,控制错误,温度影响以及老化影响。外部控制电路的有效性已可通过铣切试验证实。
在此系统中,机器人使用KuKa KR300 R2500,激光跟踪器使用带有所谓T-Cam及T-Mac的Leica AT901用以测量定位。在机器人中进行修正值的计算,通过KuKa RSI-接口输出标称位置。计算机使用Beckhoff TwinCAT作为实时系统。设备间通过EtherCAT协议进行通讯。计算机和机器人的控制系统皆是EtherCAT的主站。由于每个EtherCAT网段只允许有一个主站,计算机和机器人控制系统间的数据交换引入了esd公司的EtherCAT Slave Bridge产品ECX-EC。ECX-EC的使用可以使得两个EtherCAT网段时间同步,并使得两个EtherCAT网段之间进行数据交换,在每个循环周期中单向最大数据传输可达1024字节。
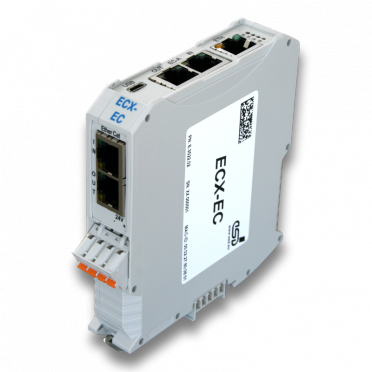
ECX-EC包含了两组EtherCAT从站接口,借助这两组接口,使得两个EtherCAT网段之间的过程数据可以进行通讯。为了确保两个EtherCAT主站的同步性,ECX-EC使用两个从站时间戳间精确的时差作为CoE对象。这样可以使得一个主站在时间上能够适应另一个主站。在时间同步冗余的情况下,ECX-EC作为第一个同时也是最后一个从站使用。因此主站可以在两个网络上同步接收从站数据。此装置遵循IEEE802.3标准,也拥有一个Ethernet接口,支持Ethernet over EtherCAT(EoE)模式,作为Switch Port来使用。固件则可以通过FoE来更新。
ECX-EC可用常用的EtherCAT软件配件工具进行配置(如esd公司的EtherCAT Workbench, Beckhoff 公司的Twin-CAT等)。作为具有坚固支撑轨道装置的ECX-EC支持DIN导轨安装标准(TS35)。
有关此产品的更多详情,请参考ecx-ec的官网信息。